My wife didn't like the stock low-back seats due to the risk of whiplash if we get rear-ended. Also, she says I snap her neck back when I accelerate hard. :innocent:
So I sold those and purchased a set of Cobra Clubman highback seats. Now the challenge is how to mount them.
The drivers side has to be adjustable so she can drive sometimes. I need the seat as far back as it will go while she needs it substantially forward to be able to reach the pedals. Luckily the passenger side can just be bolted in.
What to do?
UPDATE: I cheated. I ordered the Street Performer Seat Installation Kit from Breeze Automotive. I spent several weeks trying to make my own brackets and use the Mustang seat sliders and could never make them work.
So, my advice is, if you need to be able to move the seat fore and aft, just buy the brackets from Mark @ Breeze.
Monday, May 31, 2010
LCS or bust
In anticipation of attending the London Cobra Show I've been putting in long hours trying to get the car streetable. It won't be finished by any stretch but I'm hoping to get it put together enough to allow me to register and license it.
I mounted all of the lights to check fitment, made some adjustments, swore a bit, adjusted some more and came away with the knowledge that I'll have some serious body work to do before it gets paint.
But I couldn't drive it with green stripes all over so I bought a quart of black sealer and shot it on the body. That one change made a dramatic difference in the appearance of the body. It has a sort of ratrod look from the satin finish. It won't stay that way too long but at least it's one color. It almost looks like a car with the lights back in.
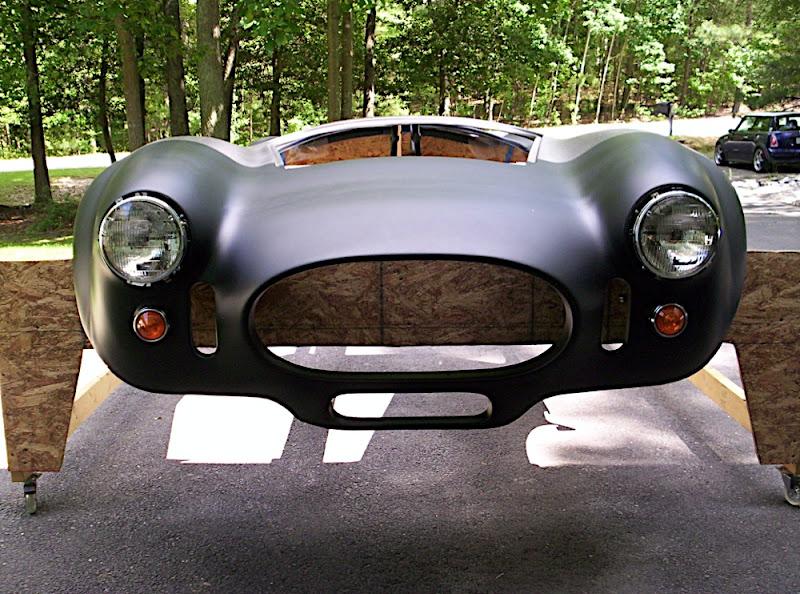
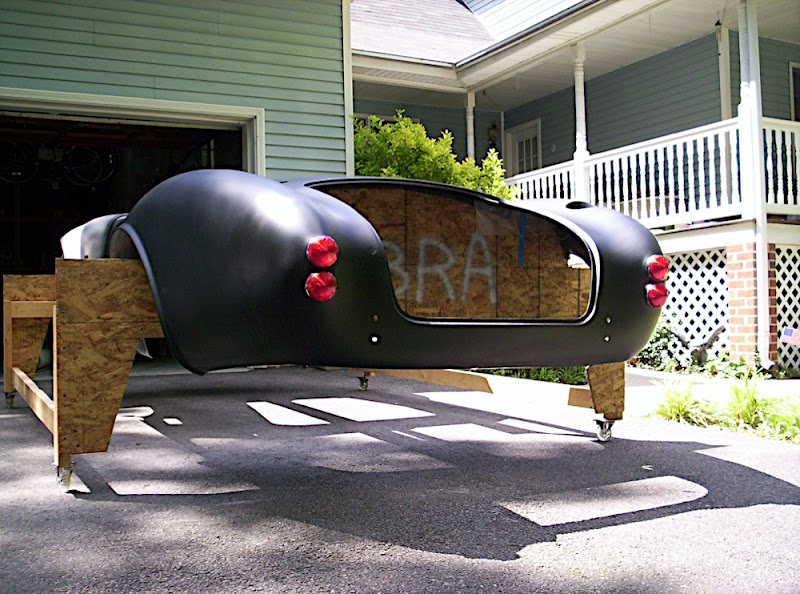
I've been working on sound and heat insulation too. ERA Replicas recommends using Frost King HVAC duct insulation. If it's good enough for them, it's good enough for me. I've done the footboxes, rear cockpit wall and transmission hump. The floorboards will be done after I figure out where to mount my seats.
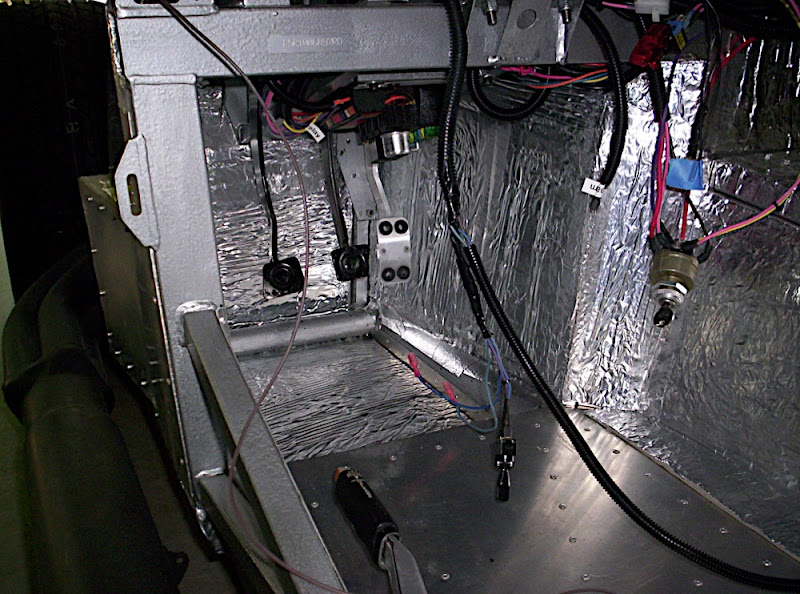
I also installed the first piece of carpet. :-D
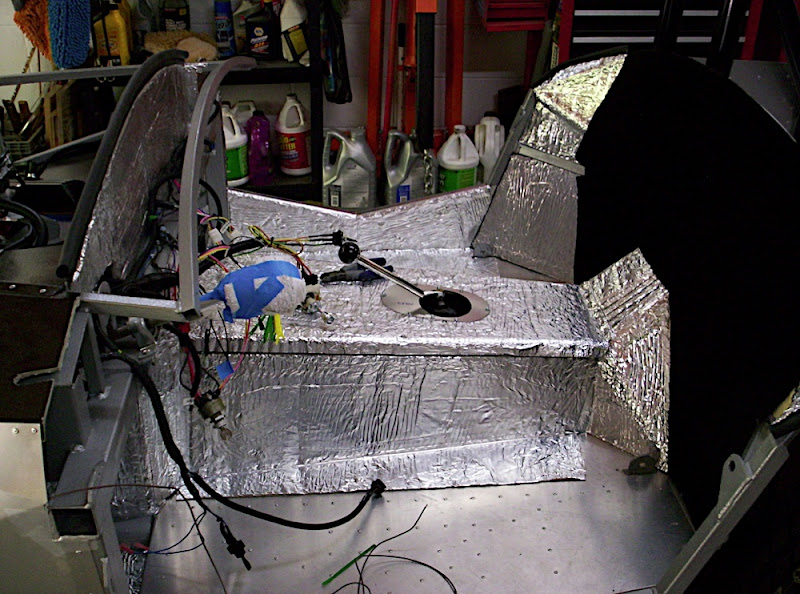
So this is how the car sits.
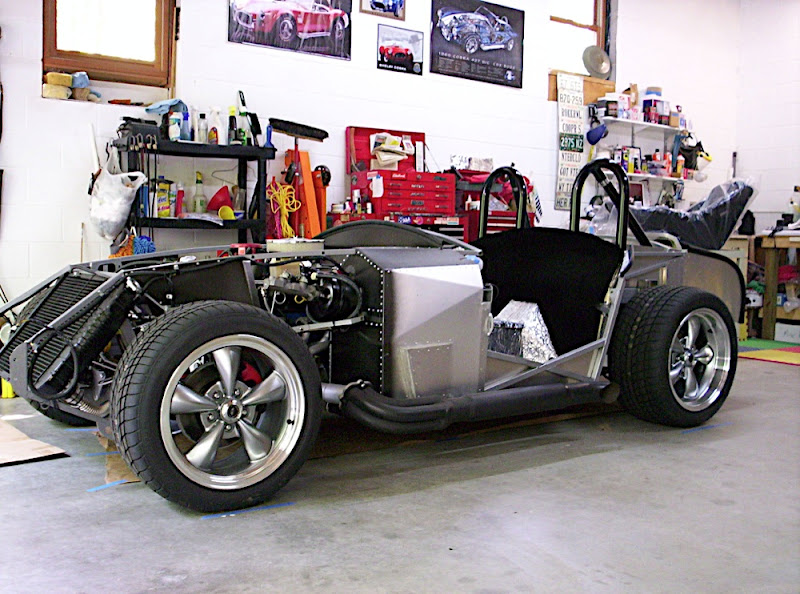
Will we make it to London? Who knows? Other life events may affect that decision. But I'm still going to try to have the car ready to go.
I mounted all of the lights to check fitment, made some adjustments, swore a bit, adjusted some more and came away with the knowledge that I'll have some serious body work to do before it gets paint.
But I couldn't drive it with green stripes all over so I bought a quart of black sealer and shot it on the body. That one change made a dramatic difference in the appearance of the body. It has a sort of ratrod look from the satin finish. It won't stay that way too long but at least it's one color. It almost looks like a car with the lights back in.
I've been working on sound and heat insulation too. ERA Replicas recommends using Frost King HVAC duct insulation. If it's good enough for them, it's good enough for me. I've done the footboxes, rear cockpit wall and transmission hump. The floorboards will be done after I figure out where to mount my seats.
I also installed the first piece of carpet. :-D
So this is how the car sits.
Will we make it to London? Who knows? Other life events may affect that decision. But I'm still going to try to have the car ready to go.
Body cutouts
I finally worked up the nerve to do the body cutouts. I had heard horror stories of how inaccurate the cutouts were from the factory so I decided I would do them on my own. It also saved me $260.
It was a bit unnerving to take a hole saw to the car but I did it figuring I can fix it if (when?) I screw something up. Happily most everything turned out.
While I had the body upside down for the Herculiner, I cut the wheelwell lips and rounded those. They almost feel like rolled aluminum now.
I also cut for the side vents and had no problems.
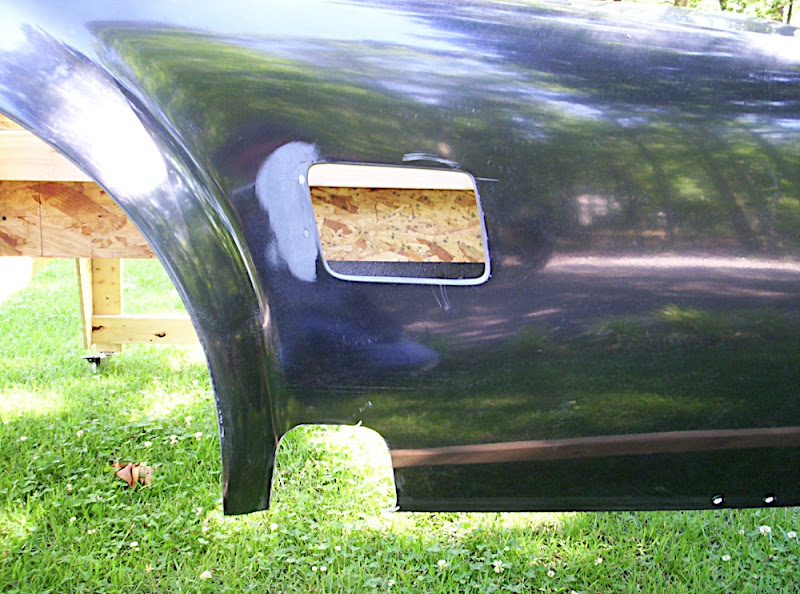
The exhaust and rollbar cutouts were a different story. FFR marks the body for us DIY cutters and stupidly I used their marks.
As a result one exhaust cutout is 0.5" forward of the other so I'll have to close that gap with some fibreglass at a later date.
The bigger issue is the rollbars. 5 holes were off by just a bit but they can be adjusted with a sanding disc and covered with a bezel. But the passenger side diagonal brace hole is just wrong. It was off to the rear by about an inch and too far to the right by another inch. But again, it's fibreglass so I can fix it. But you'd think after selling over 6000 of these kits they could mark the holes properly!
The marks of where to drill for the light mounting studs were also wrong and the screws for the taillights on one side are both at an angle. Again, I can fix it but still...
It was a bit unnerving to take a hole saw to the car but I did it figuring I can fix it if (when?) I screw something up. Happily most everything turned out.
While I had the body upside down for the Herculiner, I cut the wheelwell lips and rounded those. They almost feel like rolled aluminum now.
I also cut for the side vents and had no problems.
The exhaust and rollbar cutouts were a different story. FFR marks the body for us DIY cutters and stupidly I used their marks.
As a result one exhaust cutout is 0.5" forward of the other so I'll have to close that gap with some fibreglass at a later date.
The bigger issue is the rollbars. 5 holes were off by just a bit but they can be adjusted with a sanding disc and covered with a bezel. But the passenger side diagonal brace hole is just wrong. It was off to the rear by about an inch and too far to the right by another inch. But again, it's fibreglass so I can fix it. But you'd think after selling over 6000 of these kits they could mark the holes properly!
The marks of where to drill for the light mounting studs were also wrong and the screws for the taillights on one side are both at an angle. Again, I can fix it but still...
Gauges
I got my gauges recently. They came from Whitby Motorcars. They sell the Classic Instruments Classic Gauge set that includes the speedometer, tachometer, water temperature, oil pressure, voltmeter and fuel level gauges. I added a clock to fill the last hole in the dashboard.
When I started this build I told my wife that I one thing I had to have was a reverse reading speedometer and the Whitby kit has that. They're all electric gauges including the speedo. While this means I have to calibrate it, I won't have to change the drive gear in the transmission when I regear the rear axle - I just change some dip switches.
My workspace was the dining room table protected by an oh-so-stylish 101 Dalmatians blanket (my 21 and 25 year old sons don't want it any more for some reason.)
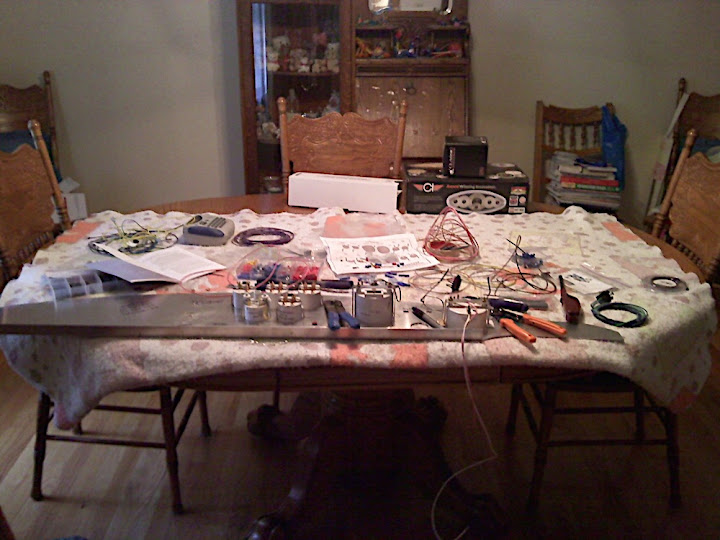
Everything went together smoothly. I used quick-disconnects in case I ever have to remove the dash. Yes, the gauges are wired together but the whole thing will unplug from the car without having to disconnect individual gauges.
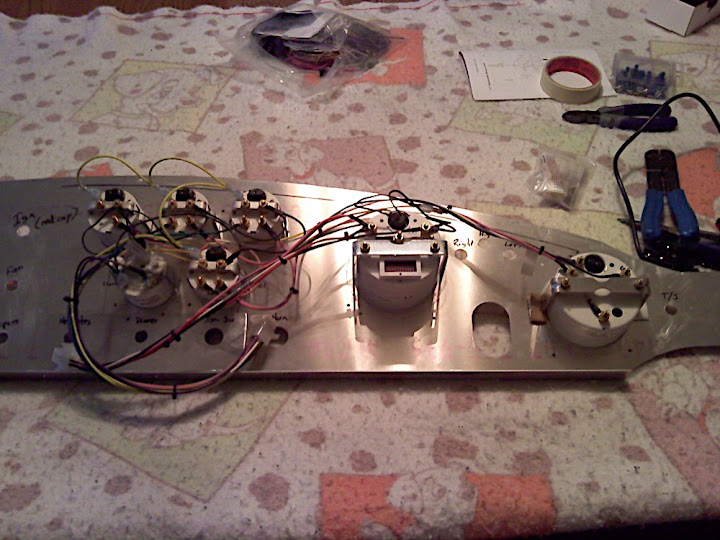
All connections were crimped, tested and shrinkwrapped. The speedometer and tachometer each have dedicated ground connections to the frame while the other gauges share their ground. Testing showed that everything worked.
Then I took it all apart so I could veneer the dash. I'm using a white oak veneer with a stain that comes close to the color of the steering wheel. Once the dash is finished and sanded I can put everything back together and install it into the car.
When I started this build I told my wife that I one thing I had to have was a reverse reading speedometer and the Whitby kit has that. They're all electric gauges including the speedo. While this means I have to calibrate it, I won't have to change the drive gear in the transmission when I regear the rear axle - I just change some dip switches.
My workspace was the dining room table protected by an oh-so-stylish 101 Dalmatians blanket (my 21 and 25 year old sons don't want it any more for some reason.)
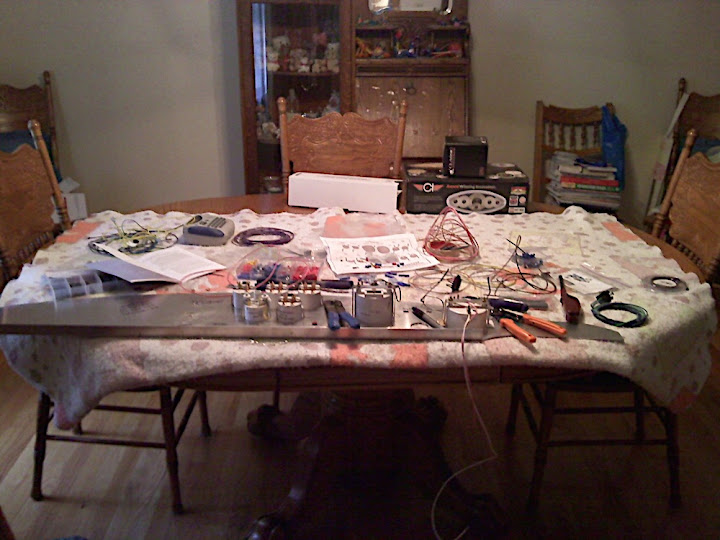
Everything went together smoothly. I used quick-disconnects in case I ever have to remove the dash. Yes, the gauges are wired together but the whole thing will unplug from the car without having to disconnect individual gauges.
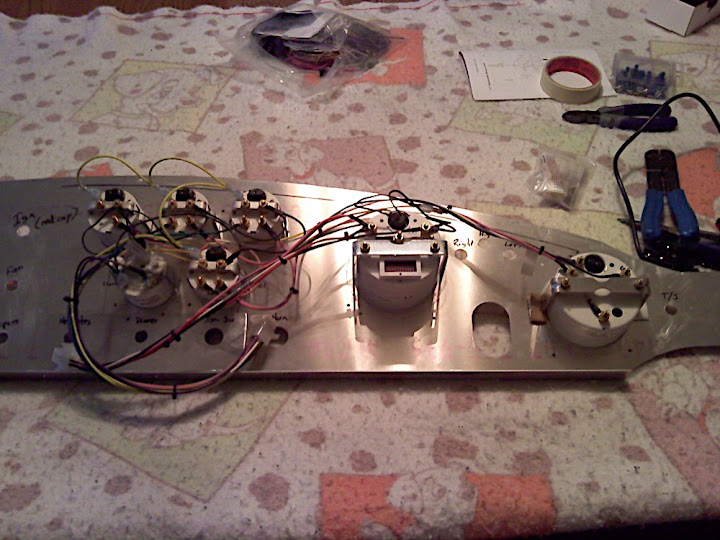
All connections were crimped, tested and shrinkwrapped. The speedometer and tachometer each have dedicated ground connections to the frame while the other gauges share their ground. Testing showed that everything worked.
Then I took it all apart so I could veneer the dash. I'm using a white oak veneer with a stain that comes close to the color of the steering wheel. Once the dash is finished and sanded I can put everything back together and install it into the car.
Wheels!!!
I've been using some extra wheels and tires to roll the chassis around during the build. They fit but they're too narrow and not the look I want for this car. Plus three of the tires are bald.
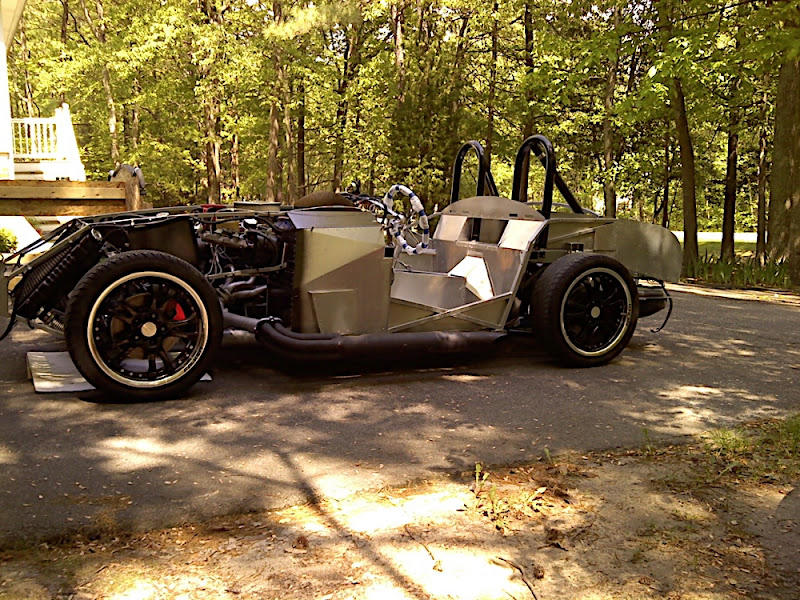
They actually belong to my youngest son but we put the stock wheels and some long-life tires on his car while he's in college. He can get the nice wheels back when he can buy some new tires.
Anyway, I finally found the wheels and tires I wanted. I ordered them from several places but it seemed that the rear wheels were on literal world backorder. Finally I found that Tire Rack had a set of American Racing Authentic Hot Rod wheels that were exactly what I wanted. They have polished lips and Anthracite spokes. The fronts are 17x9 with 245/45-17 Sumitomo HTR-Z tires. The rears are 315/35-17 HTR-Z on 17x10.5 wheels. They're a bit wider than the rollaround tires I'd been using.
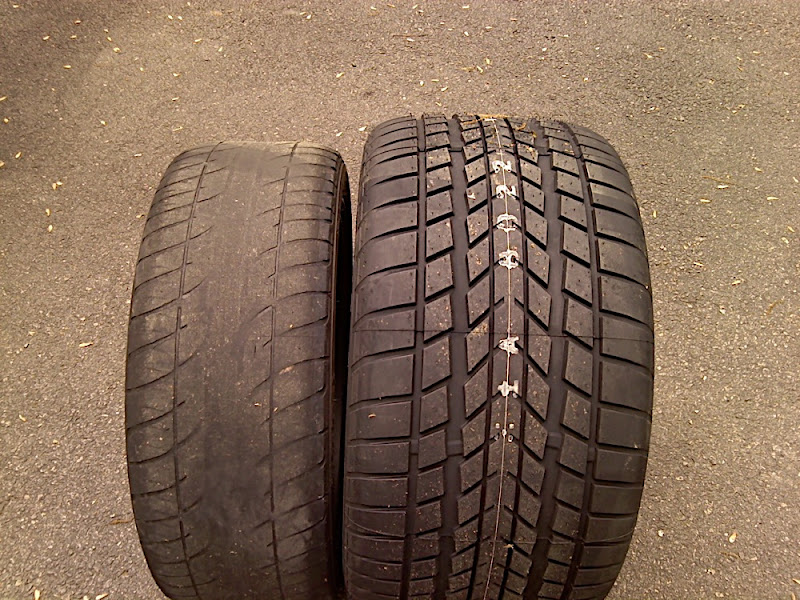
I like them!
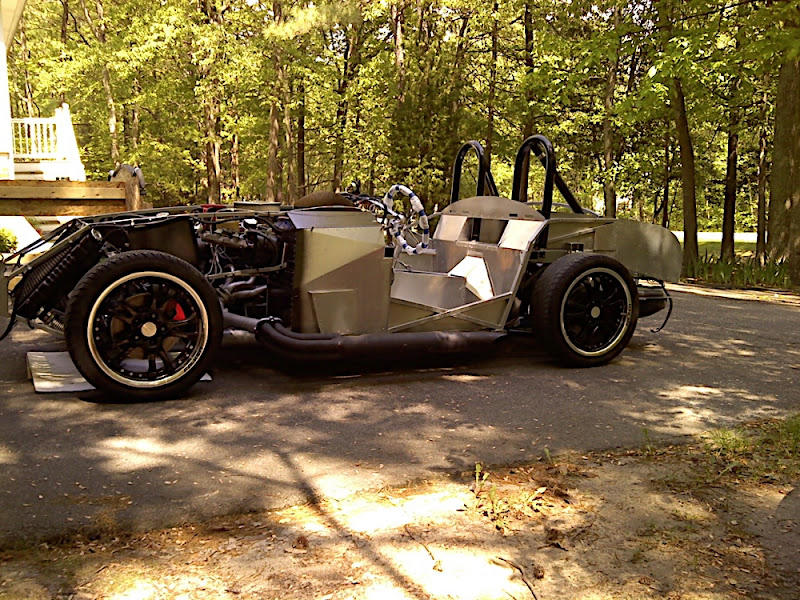
They actually belong to my youngest son but we put the stock wheels and some long-life tires on his car while he's in college. He can get the nice wheels back when he can buy some new tires.
Anyway, I finally found the wheels and tires I wanted. I ordered them from several places but it seemed that the rear wheels were on literal world backorder. Finally I found that Tire Rack had a set of American Racing Authentic Hot Rod wheels that were exactly what I wanted. They have polished lips and Anthracite spokes. The fronts are 17x9 with 245/45-17 Sumitomo HTR-Z tires. The rears are 315/35-17 HTR-Z on 17x10.5 wheels. They're a bit wider than the rollaround tires I'd been using.
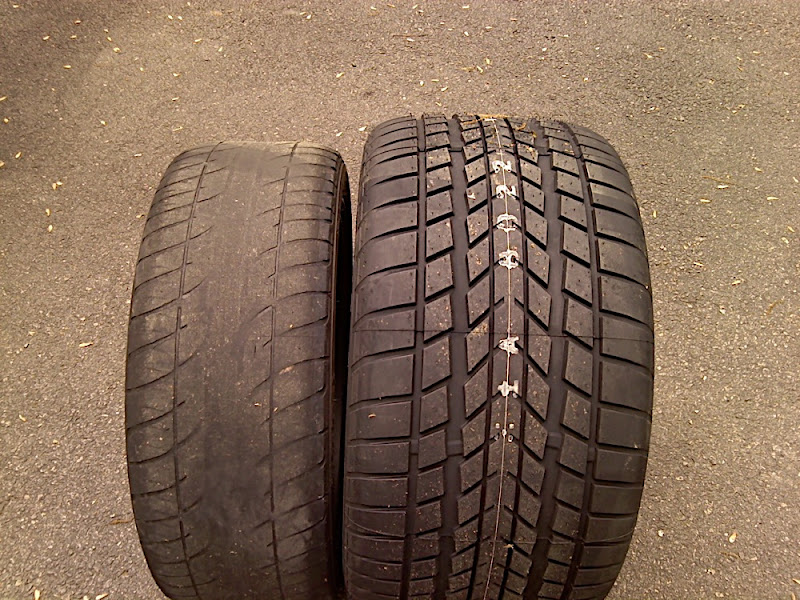
I like them!
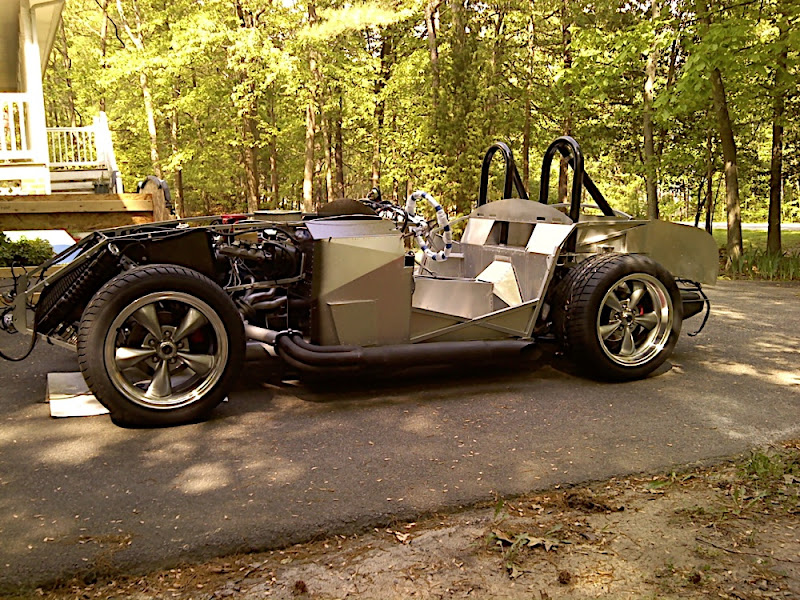
Herculiner?
Once she finished the seams I wanted to coat the underside of the body to seal it, smooth(?) it over a bit and reduce the number of fibreglass slivers that I got in my hands every time I pushed the body in or out of the garage.
What to use?
HERCULINER! It's a DIY truck bed coating. I've used it in a Jeep before and it works very well. It has ground up rubber bits in it for traction (not really important on the underside of a fibreglass body) and is tough as nails.
I laid a tarp in the yard and we pushed the body buck outside. We removed the body from it, flipped it upside down and set it on the tarp. Then I went back into the garage and laid out an old carpet. On top of the carpet went two blankets, and then I used some of the FFR shipping paper over that. Overall I had close to an inch of padding. I repositioned the body brace and we carried it into the garage.
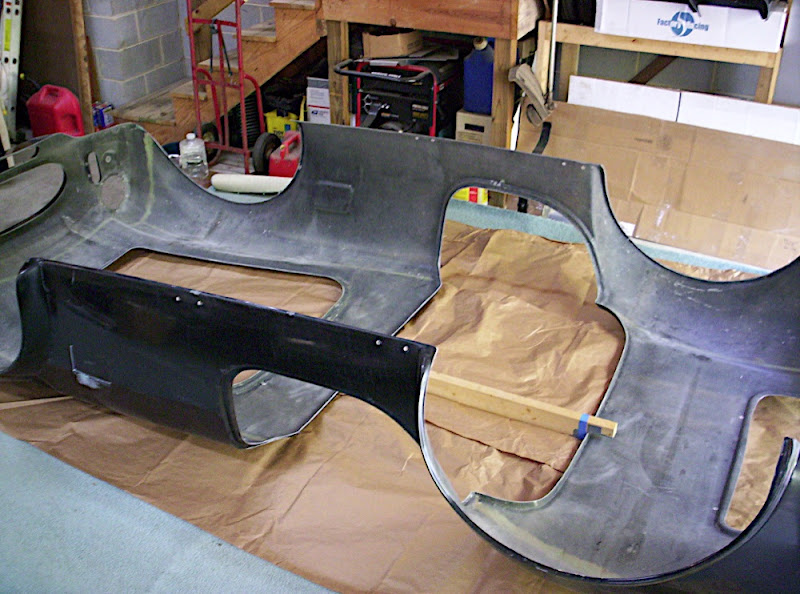
Since I hadn't done the cutting and bodywork on the edges yet, I taped them off so they didn't get coated.
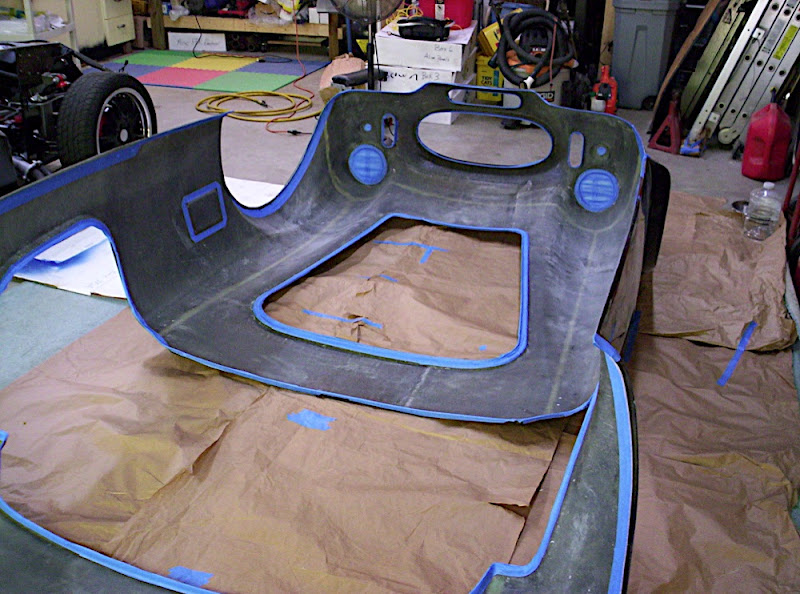
Then I got to work. Notice the gloves and old clothes. Herculiner is wondrous stuff but the only way to remove it is with Xylene before it dries. After it dries it doesn't come off. Having read horror stories of this in the past I was extra careful.
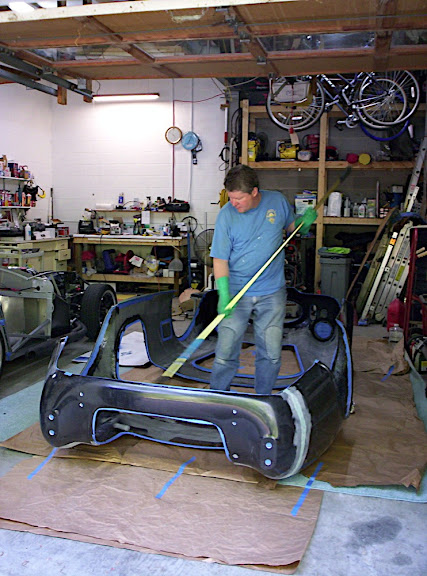
Here's an in-progress shot so show how it looks.
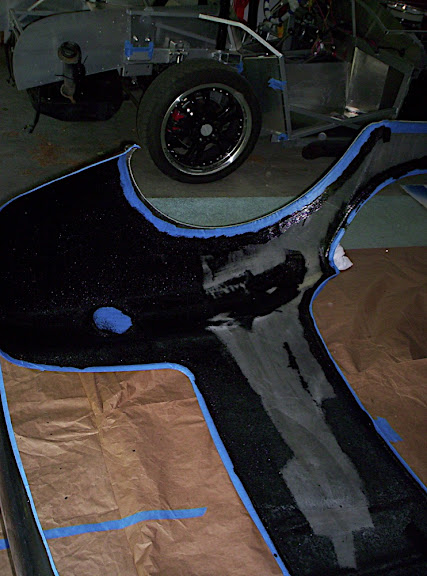
I did two coats on the whole body with an extra two in each wheelwell to reduce the probability of rock 'pings' showing in the paint later.
After it was dry I removed the tape and we flipped it back over and put it back on the body buck.
Of course, this was prior to me cutting all of the holes in the body so it now adds an extra challenge to do that. This is just another instance of me doing the right thing at the wrong time.
Oh well...
What to use?
HERCULINER! It's a DIY truck bed coating. I've used it in a Jeep before and it works very well. It has ground up rubber bits in it for traction (not really important on the underside of a fibreglass body) and is tough as nails.
I laid a tarp in the yard and we pushed the body buck outside. We removed the body from it, flipped it upside down and set it on the tarp. Then I went back into the garage and laid out an old carpet. On top of the carpet went two blankets, and then I used some of the FFR shipping paper over that. Overall I had close to an inch of padding. I repositioned the body brace and we carried it into the garage.
Since I hadn't done the cutting and bodywork on the edges yet, I taped them off so they didn't get coated.
Then I got to work. Notice the gloves and old clothes. Herculiner is wondrous stuff but the only way to remove it is with Xylene before it dries. After it dries it doesn't come off. Having read horror stories of this in the past I was extra careful.
Here's an in-progress shot so show how it looks.
I did two coats on the whole body with an extra two in each wheelwell to reduce the probability of rock 'pings' showing in the paint later.
After it was dry I removed the tape and we flipped it back over and put it back on the body buck.
Of course, this was prior to me cutting all of the holes in the body so it now adds an extra challenge to do that. This is just another instance of me doing the right thing at the wrong time.
Oh well...
More body work
My lovely wife likes to do body work, so who am I to argue. Personally I don't enjoy it much - I prefer the mechanical and fabricating stuff.
Previously I posted that she had knocked down the gelcoat seams and done a bit of grinding into the fibreglass. Then cold weather set in.
So once the weather warmed up again, she dragged out the sander and the HSRF and did some primary filling of the seams.
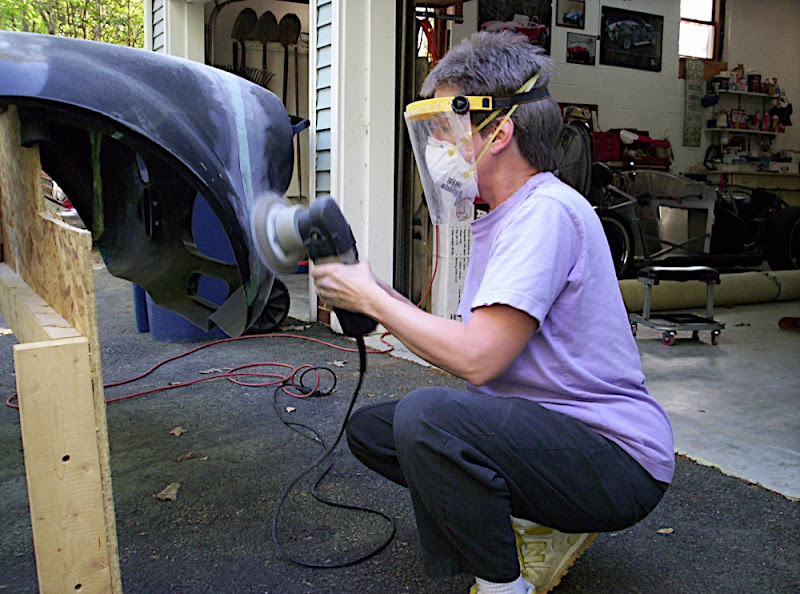
What's HSRF? 3M High Strength Marine Filler. It's a vinylester based fibreglass repair filler that's impervious to water and widely used for structural boat repairs. In our case, she used it to bring the seams back to almost level so they can be finished to the proper profile with a body filler called Evercoat Rage. Rage shouldn't be applied more than 1/4" thick so the HSRF does the structural building.
And HSRF is green, so I have green stripes all over the body now.
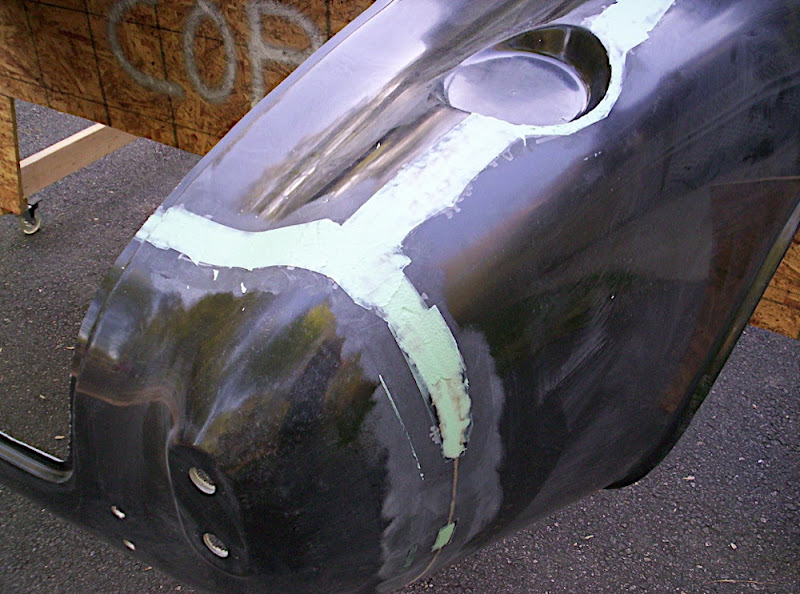
Previously I posted that she had knocked down the gelcoat seams and done a bit of grinding into the fibreglass. Then cold weather set in.
So once the weather warmed up again, she dragged out the sander and the HSRF and did some primary filling of the seams.
What's HSRF? 3M High Strength Marine Filler. It's a vinylester based fibreglass repair filler that's impervious to water and widely used for structural boat repairs. In our case, she used it to bring the seams back to almost level so they can be finished to the proper profile with a body filler called Evercoat Rage. Rage shouldn't be applied more than 1/4" thick so the HSRF does the structural building.
And HSRF is green, so I have green stripes all over the body now.
Parking brake
Since the chassis now runs and is (illegally) drivable, I figured I should have some sort of parking brake other than a block of wood.
Factory Five puts the parking brake handle in the stock Cobra location, i.e. on the right side of the transmission tunnel. There are two important points to consider about that.
First, in a right-hand drive car, it would be next to the drivers left knee and easy to release. However, in the good ol' USA, we sit on the left side of the car to drive so it's difficult to release the brake.
Second, and most important, if the driver has gone through the exercise of buckling the safety harness it's impossible to reach the brake handle to release it without unbuckling.
In reading the forums at FFCARS.COM (previously known as ffcobra.com but the name was changed due to a lawsuit by Mr. Shelby) I found that a Fiero brake handle could be used and mounted to the left of the drivers seat.
What's special about the Fiero handle to make it so desirable? It allows the brake to be set and then the handle to be pushed back down to flat, thus allowing unfettered ingress and egress to the drivers seat. To release the brake, you just pull the handle back up, push the release button and push it back down again.
No climbing over a parking brake lever and potentially hurting oneself. That's a good thing.
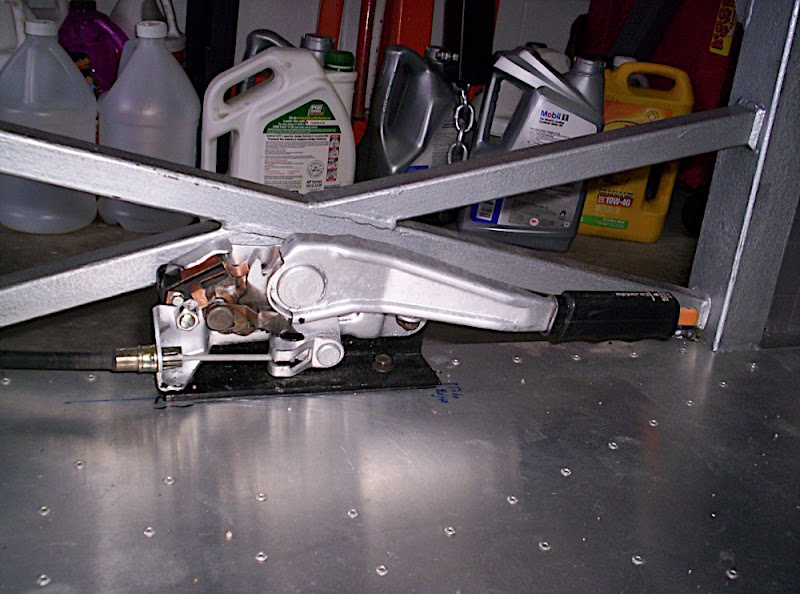
Of course, it also presents some fabrication issues since the FFR brake cable locations can't be used.
I ended up running the cable out behind the drivers seat and making a couple of brackets. One to hold the cable from the handle to the tee, and another to mount the cables that go to the brake calipers. Nothing too hard to do but there's way too much cable under there for my tastes. Someday I'll figure out the proper lengths and find someone to cut and swedge the cables.
I also had to double-over the front cable and use a clamp to attach it to the stock Mustang tee.
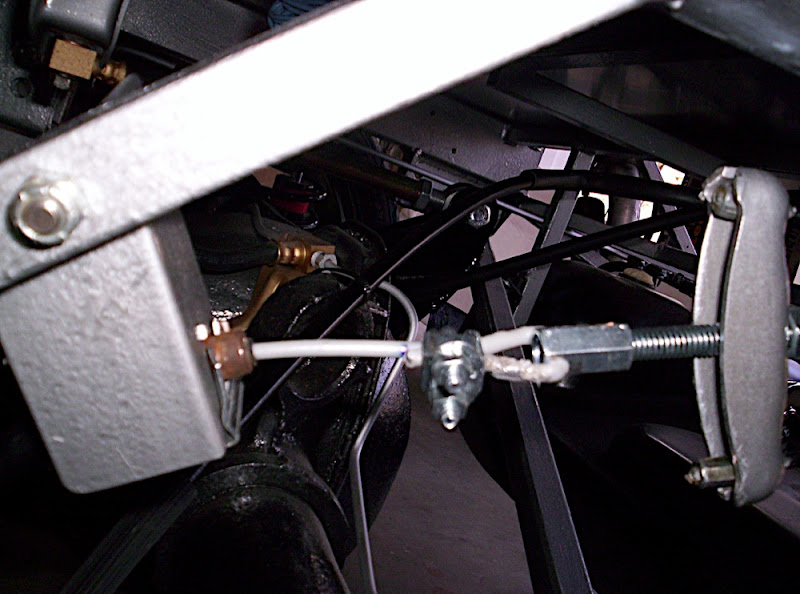
Happily it all works well and holds the car securely. The last thing I need to do is put some sort of indicator light on the dash to let me know when the brake is set. In my other cars I can just look at the handle and tell, but not this one.
Factory Five puts the parking brake handle in the stock Cobra location, i.e. on the right side of the transmission tunnel. There are two important points to consider about that.
First, in a right-hand drive car, it would be next to the drivers left knee and easy to release. However, in the good ol' USA, we sit on the left side of the car to drive so it's difficult to release the brake.
Second, and most important, if the driver has gone through the exercise of buckling the safety harness it's impossible to reach the brake handle to release it without unbuckling.
In reading the forums at FFCARS.COM (previously known as ffcobra.com but the name was changed due to a lawsuit by Mr. Shelby) I found that a Fiero brake handle could be used and mounted to the left of the drivers seat.
What's special about the Fiero handle to make it so desirable? It allows the brake to be set and then the handle to be pushed back down to flat, thus allowing unfettered ingress and egress to the drivers seat. To release the brake, you just pull the handle back up, push the release button and push it back down again.
No climbing over a parking brake lever and potentially hurting oneself. That's a good thing.
Of course, it also presents some fabrication issues since the FFR brake cable locations can't be used.
I ended up running the cable out behind the drivers seat and making a couple of brackets. One to hold the cable from the handle to the tee, and another to mount the cables that go to the brake calipers. Nothing too hard to do but there's way too much cable under there for my tastes. Someday I'll figure out the proper lengths and find someone to cut and swedge the cables.
I also had to double-over the front cable and use a clamp to attach it to the stock Mustang tee.
Happily it all works well and holds the car securely. The last thing I need to do is put some sort of indicator light on the dash to let me know when the brake is set. In my other cars I can just look at the handle and tell, but not this one.
Exhaust
The go-cart run was done with an unpainted exhaust as it came from Factory Five. Once the weather warmed up I pulled the sidepipes back off and did some cleaning and sanding. I was surprised at how much surface rust had formed on the pipes, especially anywhere I had touched them.
I sanded them with 320 grit paper and wiped them down with acetone. Then came the challenge of how to paint them.
Since the body buck was in the lowered position I had the stilts available. I used them to build a temporary rack and hung the pipes from that so I could paint them.
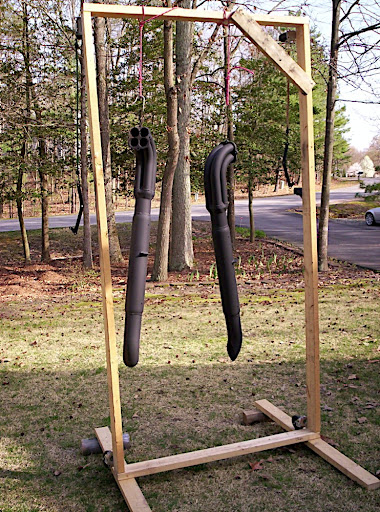
You can see that the wheels are still on the rack as I knew this was just a short term solution and I'd need to put the body back up later.
Anyway, the pipes are now a nice flat/satin black and hopefully there will be no more rust problems.
Eventually, when the packing burns out, I'll replace the actual muffler part and I may get them ceramic coated but for now this is cheap, looks okay and can be touched up easily.
I sanded them with 320 grit paper and wiped them down with acetone. Then came the challenge of how to paint them.
Since the body buck was in the lowered position I had the stilts available. I used them to build a temporary rack and hung the pipes from that so I could paint them.
You can see that the wheels are still on the rack as I knew this was just a short term solution and I'd need to put the body back up later.
Anyway, the pipes are now a nice flat/satin black and hopefully there will be no more rust problems.
Eventually, when the packing burns out, I'll replace the actual muffler part and I may get them ceramic coated but for now this is cheap, looks okay and can be touched up easily.
Go-cart!
After I got the engine running and tied up more than a few loose ends on it, I got a chance to run the chassis up and down the street as a go-cart. I don't have any video but my lovely wife took a few pictures to commemorate the event.
Here's my first pass down the street.
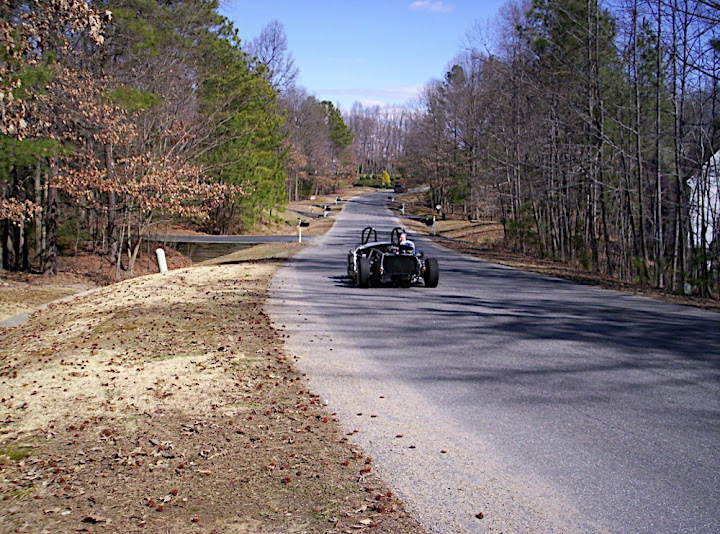
And pulling back into the driveway.
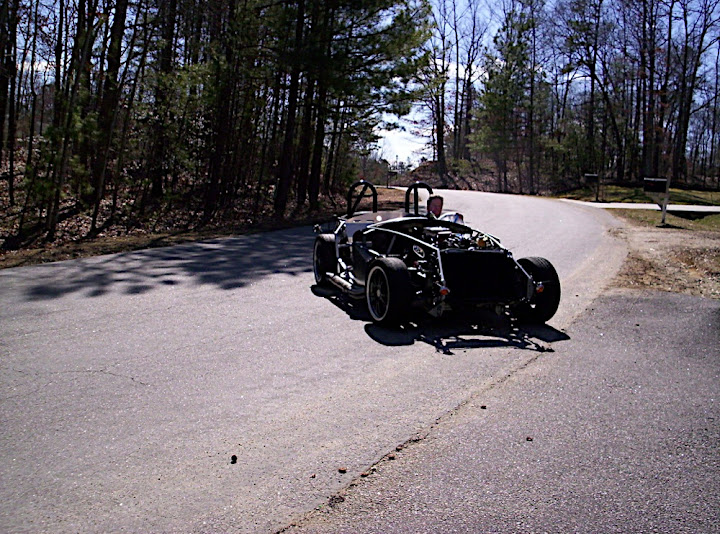
The only gauge I was running at the time was a mechanical oil pressure gauge so I had to be careful not to run the engine too long or too hard since I didn't know how hot it would get.
But this thing is QUICK and I never got past 1/4 throttle.
Here's my first pass down the street.
And pulling back into the driveway.
The only gauge I was running at the time was a mechanical oil pressure gauge so I had to be careful not to run the engine too long or too hard since I didn't know how hot it would get.
But this thing is QUICK and I never got past 1/4 throttle.
It seems like forever...
since I updated this blog. Well, it's been 5 months anyway.
Winter presented too much cold weather to work in my unheated garage very much and I've been trying to catch up since it warmed up, thus the lack of updates.
Anyway, I'm going to try to get everything up-to-date today and get back on track with regular updates again.
Winter presented too much cold weather to work in my unheated garage very much and I've been trying to catch up since it warmed up, thus the lack of updates.
Anyway, I'm going to try to get everything up-to-date today and get back on track with regular updates again.
Subscribe to:
Posts (Atom)